07. Punch Board / Player Board | v.20221215
2.2.2.7 Punch Board / Play
2.2.2.7.1 • The Material Issue
- CCNB is unfit for digital printing. If this is selected, art paper will be applied instead.
- 300gsm art paper will be applied instead of 350gsm as this exceeds the maximum thickness for the digital printer.
2.2.2.7.2 • Color Difference Issue
- There will be a color discrepancy as the sample is manufactured using digital printing, while mass production will be completed using a real printing machine. The digital printed sample will be around 85%~90% similar to the mass production version.
2.2.2.7.3 • The Varnishing Issue
- The sample surface cannot be protected by varnishing as it is pressed by the digital printer. As such, the surface will get scratched, faded and easily stained. This is inevitable in digital printing; however, it will be avoided in mass production.
2.2.2.7.3 • Example of varnish issue
2.2.2.7.4 • The Lamination Issue
- The following will occur during the pre-production process if only a small number of samples are created, as the pressure and temperature can’t be adjusted to a stable state in such a short period of time.
- Unft and bubbling (this cannot be avoided in the sample printing, however it will not occur in mass production.)
- Whiting and blurring (this cannot be avoided in the sample printing, however it will not occur in mass production.)
2.2.2.7.5 • Paper Pasting (mounted) Defect
- The pattern on the front and back of the punch-board may deviate (it is even worse when linen texture is required). This is caused by the high humidity within the paper during a comparatively short pre-production period, in which the paper can easily be expanded or stretched. This leads to the misalignment of the pattern.
An additional process of dehumidifcation will be used during mass production (at least a 24 hour dehumidifcation period). This will reduce such defects by controlling the humidity of the paper.
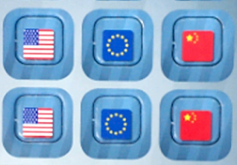
2.2.2.7.5 • Example of paper pasting defect
2.2.2.7.6 • The Layering Issue
- When the punch boards are punched out, issues such as layering or rough edges may occur. This is caused by the high humidity of grey boards during a comparatively short pre-production period. An additional process of dehumidification will be used during the mass production (at least a 24-hour dehumidification period). This will reduce such defects by controlling the humidity of the paper.
2.2.2.7.6 • Example of layering issue
2.2.2.7.7 • Die Cut Holder Issue
- Die-cut holders are added to the die-cut line as connections between the board and tokens.
This prevents the punched tokens from disconnecting veasily, which may embed and damage the die cut mold.